In modern precision manufacturing, accuracy and consistency are more than just goals—they’re fundamental requirements. Whether producing aerospace parts, automotive components, or medical devices, manufacturers must ensure that every feature of a part meets exact design specifications. This is where Geometric Dimensioning and Tolerancing (GD&T) comes into play. If you’re wondering what is gd&t, this guide will help you understand its definition, purpose, and real-world applications.
GD&T is not just a technical tool for engineers; it’s a universal language that helps communicate design intent clearly and accurately across every phase of production. From designers and machinists to quality control and inspectors, GD&T eliminates ambiguity and drives alignment throughout the manufacturing process.
Understanding GD&T: The Basics
Geometric Dimensioning and Tolerancing (GD&T) is a symbolic language used in engineering drawings to define the shape, orientation, size, and location of features on a part. It replaces or enhances traditional coordinate dimensioning by focusing on how features function and relate to one another in a three-dimensional space.
Governed by standards such as ASME Y14.5 or ISO 1101, GD&T uses a set of standardized symbols to communicate allowable geometric variation, enabling parts to fit together and perform correctly even with minor manufacturing deviations.
Why GD&T Is Important in Manufacturing
Traditional dimensioning methods rely on linear measurements and fixed tolerances. While this can be effective for simple parts, it falls short in complex designs where multiple surfaces and features must interact precisely. Without GD&T, interpretation can vary between designers, machinists, and inspectors—leading to miscommunication, errors, and rework.
GD&T provides a more robust solution by:
-
Defining functional limits based on part use
-
Communicating design intent with clarity
-
Reducing ambiguity in drawings
-
Improving inspection and verification processes
-
Supporting lean manufacturing and reduced waste
Core Elements of GD&T
GD&T combines several core concepts into a unified system for controlling geometry. Below are the main elements you need to understand.
1. Feature Control Frame (FCF)
The Feature Control Frame is the rectangular box that specifies the geometric control applied to a feature. It contains three pieces of information:
-
The geometric characteristic symbol (e.g., flatness, position)
-
The tolerance value (e.g., 0.02 mm)
-
The datum references (when applicable)
This indicates a positional tolerance of 0.02 mm relative to datums A and B.
2. Datums and Datum Features
A datum is a reference point, axis, or plane from which measurements are made. Datums provide a standardized framework for part inspection and assembly. The more complex a part, the more important datums become to ensure consistency.
3. Tolerance Zones
Every geometric control in GD&T defines a specific type of tolerance zone—such as a flat plane for flatness, a cylinder for position, or a circular band for circularity. These zones determine the acceptable variation in part features.
GD&T Symbols and Their Classifications
GD&T includes 14 standard symbols grouped into five categories. Each symbol defines a different type of control on a part’s feature.
● Form Controls
-
Straightness
-
Flatness
-
Circularity (Roundness)
-
Cylindricity
● Profile Controls
-
Profile of a line
-
Profile of a surface
● Orientation Controls
-
Angularity
-
Perpendicularity
-
Parallelism
● Location Controls
-
True position
-
Concentricity
-
Symmetry
● Runout Controls
-
Circular runout
-
Total runout
Each of these plays a role in ensuring a part’s ability to function properly in its assembled state.
Real-World Application of GD&T
Let’s consider a practical example: a machined hole that will receive a pin. Without GD&T, you might specify the hole diameter and its X and Y position using basic tolerances. However, this method does not control how the hole aligns relative to other features or axes.
With GD&T, you can apply a true position tolerance that controls not only the size but the exact spatial location of the hole within a defined 3D tolerance zone. This ensures better fitment and reduces the likelihood of assembly issues.
Benefits of GD&T for Engineers and Manufacturers
1. Improved Communication Across Teams
GD&T provides a consistent and standardized way to convey design intent, reducing errors between design, machining, and inspection teams.
2. Function-Driven Tolerancing
Instead of applying the same tight tolerances to every feature, GD&T allows you to prioritize critical features and apply functional tolerancing where needed. This reduces unnecessary manufacturing costs.
3. Efficient Inspection and Quality Control
GD&T simplifies part inspection using CMMs (Coordinate Measuring Machines) and other metrology tools that can automatically verify parts against tolerance zones.
4. Cost Savings
By applying tolerances based on function rather than habit, GD&T reduces scrap, rework, and excessive tooling costs while maintaining quality.
Industries Where GD&T Is Essential
GD&T is commonly used in industries where tight tolerances and precision matter:
-
Aerospace: Controls alignment of turbine blades, structural fasteners, and flight-critical parts.
-
Automotive: Ensures precision in engine blocks, transmission assemblies, and suspension systems.
-
Medical Devices: Verifies accuracy of surgical instruments, implants, and diagnostic equipment.
-
Energy: Supports precise fabrication of valves, connectors, and pumps used in high-pressure environments.
-
Defense and Robotics: Ensures structural fitment and movement for advanced weaponry and automation systems.
Common GD&T Misconceptions
Some manufacturers hesitate to use GD&T due to misconceptions:
-
“It’s too complicated.” GD&T has a learning curve, but with training, teams become more efficient and aligned.
-
“It’s only for big companies.” Even small shops benefit from reduced rework and better communication.
-
“Only inspectors need to understand it.” In reality, everyone from design to machining plays a role in interpreting and applying GD&T.
How to Start Implementing GD&T
For organizations new to GD&T, here are key steps to start adoption:
-
Educate your team: Train engineers, machinists, and inspectors in GD&T fundamentals.
-
Use compatible software: Modern CAD tools support GD&T features and make annotation easier.
-
Invest in inspection tools: CMMs and vision systems can automatically measure GD&T-based features.
-
Apply gradually: Start with mission-critical features and expand as your team gains confidence.
The Future of GD&T in Smart Manufacturing
As the industry shifts toward digital manufacturing, GD&T is becoming even more relevant. Model-Based Definition (MBD) enables embedding GD&T directly into 3D CAD models, eliminating the need for 2D drawings. This integration enhances automation, ensures design traceability, and improves workflow efficiency.
In addition, with the rise of digital twins and AI-driven inspection, GD&T will continue to play a pivotal role in enabling real-time verification and optimization in manufacturing environments.
Conclusion
Understanding what is gd&t is essential for anyone involved in the design, manufacturing, or inspection of precision parts. GD&T ensures that every component fits, functions, and performs as intended—regardless of the complexity of the part or assembly.
By reducing ambiguity, improving communication, and supporting cost-efficient tolerancing, GD&T has become a core tool for modern engineering. As manufacturing evolves, GD&T will remain an integral part of producing reliable, high-quality components across industries.
- The Future of GD&T in Smart Manufacturing,
- Wondering what is GD&T? Learn how Geometric Dimensioning and Tolerancing improves part accuracy, reduces manufacturing errors, and supports precision in engineering design.
- The Future of GD&T in Smart Manufacturing,
Related posts:
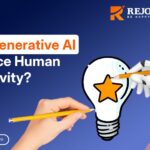
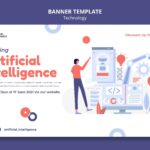
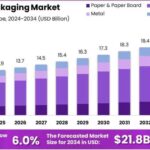
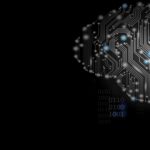
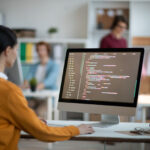
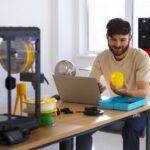
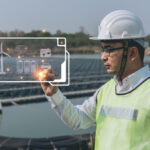
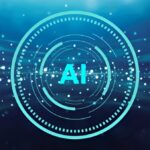