When Rajiv started as a trainee on the floor of a major auto plant a decade ago, the work was still a mix of human skill and old-school machinery. He remembers watching operators install dashboards by hand, double-checking every bolt before a car moved on.
These days, when he visits that same facility, the difference is almost unbelievable. Robots glide between workstations carrying parts. Automated arms install components with millimeter precision. Screens above each line track production in real time.
This is the era of automotive smart manufacturing, a world where software, sensors, and robotics have redefined how cars are built.
Whether you’re an engineer, business leader, or just fascinated by technology, understanding the systems behind these changes is essential. Let’s explore the key technologies making this transformation possible and why they matter so much.
What Is Automotive Smart Manufacturing?
In simple terms, it’s the fusion of advanced technologies to create more efficient, flexible, and data-driven production processes.
Instead of relying only on human labor and standalone machines, automotive smart manufacturing brings together:
- Connected equipment that shares information in real time.
- Automation that reduces errors and boosts output.
- Analytics tools that predict problems before they happen.
This integrated approach isn’t just about building cars faster, it’s about building them better.
1. Industrial IoT and Sensor Networks
The Internet of Things (IoT) is at the heart of modern manufacturing. Hundreds of sensors track temperature, torque, vibration, and other parameters across a plant.
In an automotive context, IoT makes it possible to:
- Monitor assembly lines in real time.
- Measure wear and tear on tools.
- Automate maintenance alerts before equipment fails.
Imagine a robot arm installing windshields. With IoT sensors, managers can spot subtle shifts in pressure or alignment and adjust immediately. That reduces waste and keeps quality consistent. This level of visibility is a huge leap from the old days of manual inspections.
2. Advanced Robotics and Cobots
Industrial robots have been around for decades. But today’s robots are smarter, more adaptable, and easier to integrate into workflows.
Modern automotive smart manufacturing relies on:
- Multi-axis robots that handle complex assembly.
- Vision-guided systems that “see” parts for precise placement.
- Collaborative robots, known as cobots, that safely work side by side with people.
Cobots are especially important. They can assist with repetitive or heavy tasks without replacing workers entirely. For example, a cobot might hold a door panel steady while a technician secures bolts.
The result? Fewer injuries, faster cycles, and more consistent builds.
3. Additive Manufacturing (3D Printing)
3D printing isn’t just for prototypes anymore. Automakers now use additive manufacturing to produce jigs, fixtures, and even end-use components.
Why does this matter? Because it:
- Speeds up production of custom tools.
- Cuts costs on low-volume parts.
- Reduces material waste.
If a line needs a specialized bracket or fitting, engineers can design and print it in days instead of waiting weeks for suppliers.
In some cases, automakers are even 3D printing components like ducts or housings directly into vehicles.
4. Artificial Intelligence and Machine Learning
AI has become a driving force in automotive smart manufacturing. It helps factories make sense of all the data IoT devices collect.
Machine learning models analyze information to:
- Predict when equipment will fail.
- Optimize production schedules.
- Detect defects early.
For example, AI-powered cameras can scan welds for tiny imperfections invisible to the human eye. When the system finds an anomaly, it alerts staff immediately so they can fix the problem before the vehicle moves forward.
This level of insight improves quality while reducing rework costs.
5. Digital Twins
Imagine having a virtual replica of your entire factory. That’s the idea behind digital twins.
A digital twin combines real-time sensor data with 3D models to create a living simulation of production lines, equipment, and processes.
With a digital twin, managers can:
- Test process changes virtually before applying them in real life.
- Model “what if” scenarios to spot potential bottlenecks.
- Train employees on simulated systems.
In the automotive world, digital twins can even follow a vehicle through production, tracking everything from paint thickness to torque settings.
This technology transforms decision-making from guesswork to evidence-based strategy.
6. Cloud Computing and Edge Processing
All this data needs somewhere to go. Cloud platforms collect, store, and analyze information from across the plant.
At the same time, edge computing, processing data close to where it’s generated, ensures real-time performance.
This combination allows automotive smart manufacturing teams to:
- Visualize operations on dashboards anywhere in the world.
- Share insights across departments.
- React instantly to changing conditions on the floor.
Cloud tools also make it easier to collaborate with suppliers, partners, and customers.
7. Augmented Reality (AR) and Virtual Reality (VR)
Training and maintenance are faster when teams can see information overlaid on the real world.
With AR, a technician wearing smart glasses can:
- Access step-by-step instructions.
- View sensor data in their field of vision.
- Get remote guidance from experts.
VR, on the other hand, helps engineers design production lines or simulate workflows before any equipment arrives.
Both technologies reduce errors and shorten learning curves.
8. Cybersecurity Systems
The more connected factories become, the more vulnerable they are to cyber threats.
Automakers invest heavily in cybersecurity measures to:
- Protect intellectual property.
- Safeguard production schedules.
- Keep critical systems running.
Firewalls, encryption, and secure access controls are all standard parts of any smart manufacturing strategy.
Why These Technologies Matter
Together, these innovations make factories:
- More agile: They can adapt quickly to new models or customer demands.
- More efficient: Automation reduces downtime and waste.
- More resilient: Data-driven insights help spot problems early.
Ultimately, automotive smart manufacturing gives companies an edge in a fiercely competitive market.
A Real-World Snapshot
Let’s look at a real example.
BMW’s plant in Regensburg, Germany, uses:
- Digital twins to model production.
- 3D printing to create tools.
- AI to inspect welds.
- Cobots to assist workers.
The result? More than 300,000 cars built every year with fewer defects and faster cycle times. This is what the future of manufacturing looks like, and it’s already here.
Final Thoughts
The automotive industry has always been a proving ground for innovation. From the first assembly lines to today’s data-driven factories, the sector keeps raising the bar. If you work in manufacturing, engineering, or technology, now is the time to understand these systems. Learning how automotive smart manufacturing works can help you stay relevant and find new ways to contribute.
- Key Technologies Powering Automotive Smart Manufacturing Today
- Learn which technologies are driving automotive smart manufacturing, from AI and IoT to robotics and data analytics, to improve efficiency and product quality.
- Digital Transformation, Smart Manufacturing, Industry 4.0
Related posts:
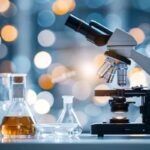
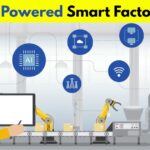
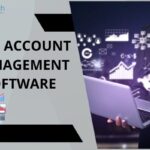

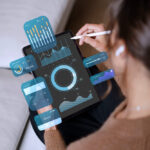

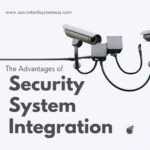
